NavVis Helps Audi Germany Neckarsulm Factory Realize Digital Transformation
Since 1899, Audi brand has become synonymous with high-performance cars with its outstanding manufacturing quality and innovative design. The company is active in more than 100 markets around the world, providing customers with about 1.8 million brand-new Audi cars in 2019.
Audi's legendary corporate philosophy Vorsprung durch Technik (breakthrough technology, enlighten the future) explains Audi's longevity and success——a recent example is the digitization of its production workshop and buildings in Neckarsulm.

Challenge: New Vision of Production Planning
Audi currently employs nearly 90,000 people worldwide, of which about 60,000 work in factories in Ingolstadt and Neckarsulm, Germany. "Virtual planning has certainly been our topic for many years," said Bernd Widdmann, who is in charge of process planning in the assembly department of the Ingolstadt and Neckarsulm factory.
.
▲Audi's factories in Ingolstadt and Neka sulm
Widdmann explained that at the beginning, the field focused on body workshops, where large robots were used to assemble several parts. However, today, this virtual planning is also being considered for final assembly, and many models are produced by robots in cooperation with employees. Production processes can now be completely planned, optimized and simulated on computers.
▲Audi's Neckarsulm factory in Germany realized digital transformation with NavVis solution.
Reality capture comes in handy with its ability to create virtual models of production sites.T The virtual model can be used as a reliable basis for production planning without actually being carried out on the production site. The task of exploring this exciting possibility falls on project manager Andr é Bongartz and his team. Since 2017, they have cooperated with NavVis to find a method to integrate the point cloud data generated by NavVis mobile scanning system with Neckarsulm's existing planning system.
Solution: 1000 square meters of scanning per hour
" I probably know more about the assembly of the Audi A6 than most A6 fitters do today. "Alperen Ö zt ü rk said. He He wheeled the Navvis M6 indoor mobile scanner through the sprawling manufacturing floor .He used to work in Audi A8 assembly line.
The total area and time scanned so far has been 250 hours to scan 250,000 square meters, or 34 working days. That equates to about 1,000 square meters per hour. Ö zt ü rk pushed the mobile scanning equipment through each room at walking speed. A laser scanner above his head captures the surrounding area as he moves, and the initial outline of the area covered by the scan is immediately visible on the display.In a very short time, accurate digital images of existing buildings will be created.
▲Plant planning using measurement tools in NavVis IndoorViewer
Results: Machine Learning and Point Cloud
After the scanned data has been post-processed and presented on the NavVis IndoorViewer, Stakeholders can use any standard web browser on a computer, tablet or smartphone to navigate the virtual manufacturing floor..Users can look around and enlarge production lines and machines. Key details are clearly visible and can be highlighted by means of points of interest.
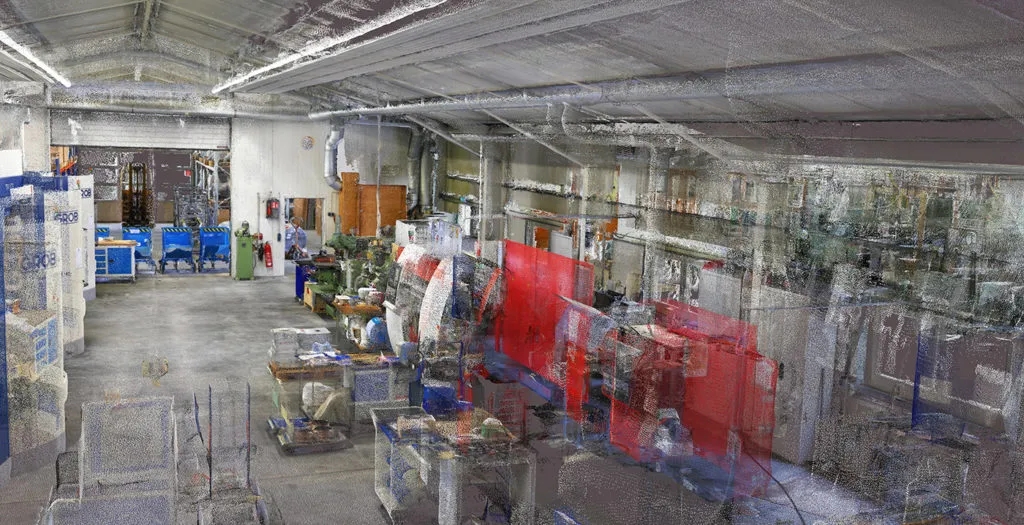
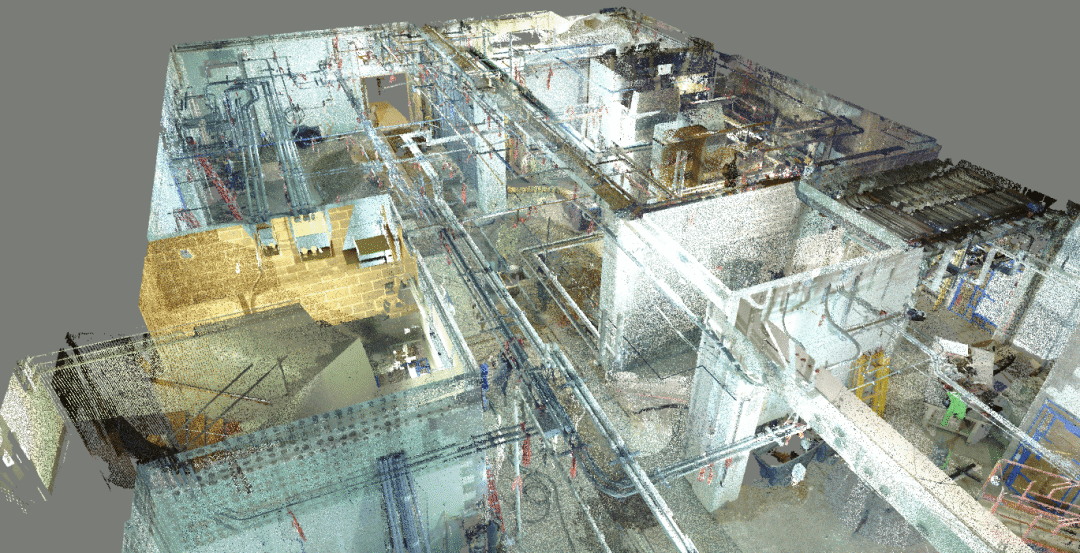
At the same time, another benefit of a mobile scanning system is that it generates a point cloud that records every machine and system.With the help of machine learning, the point cloud is then integrated into the CAD model of the digital factory to allow virtual access and monitoring of the entire workshop (including all machines, systems, and shelves).
This saves Audi employees a lot of time and cost, and achieves the production planning goal independent of the site. "Our digital planning system offers great advantages, especially during the Novel Coronavirus pandemic," Bongartz explained.
"Even during home work, Our plant planners are also able to conduct plant measurements without on-site or even with a scale."——Andr é Bongartz Process Planning Method/Standard
"Even during home work, our plant planners are also able to conduct plant measurements without on-site or even with a scale.These measurements will then be used to remotely create highly accurate facility plans. "
Future Applications
For the next step, it is planned to carry out digital scanning of all production workshops in Neckarsulm factory, and then in the neighboring Ingolstadt factory. When the factory buildings there also allow virtual access, business trips to other factories around the world will become unnecessary.
Another possible application of the data generated by NavVis M6 is a virtual factory visit. In the foreseeable future, customers planning to buy new cars may be able to wear 3D glasses to cross the assembly line and and get an insight into areas that were previously closed to the public.
These virtual Tours still need to be considered for data protection. As Andr é Bongartz explained: "Even when production comes to a standstill, there are always people moving in these halls." Therefore, no one should be recognized in the panoramic image, and all faces will be automatically blurred.